Projects
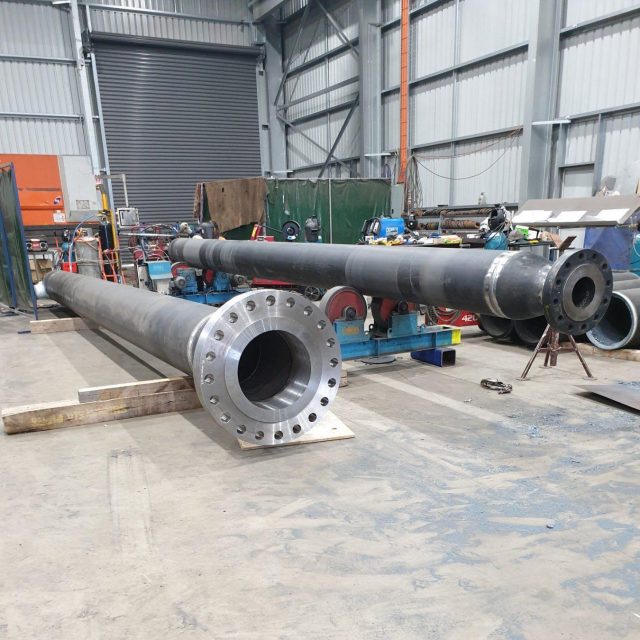
Katnook Gas Processing Facility
Clients > Beach Energy and Enscope
Project Year > 2019 - 2020
Beach Energy redevelopment of the Katnook Gas Processing Facility (KGPF). The project site is in the Otway basin adjacent to the Ladbroke Grove Power Station in South Australia, approximately 40 km North of Mount Gambier.
DMK Engineering completed three major project portions along with numerous supporting packages. The largest being the supply and fabrication of pipe support structures, the fabrication, testing and coating of all process piping and the supply of labour, equipment and materials for installation of all structural, mechanical and piping components at the site.
Project scope and highlights:
- Pre project cleaning, hydrostatic testing and local support for intelligent pigging / scanning of existing well to plant flow line piping.
- Fabrication and surface treatment of Pipe Supports
- Fabrication of stainless steel, carbon steel and A333 Grade 6 low temp spec piping, including heavy wall 500nb Sch 100 process spools.
- Surface Treatment of Carbon Steel Pipework
- Over 1400 fully traced welds, including tracking of field welds for piping installation.
- 1400+ welds Visual, Magnetic Particle, Radiographic and Ultrasonic inspection and testing, zero project weld failures detected.
- Refurbishment of project process tanks, volume up to 150kL, including on-site and off-site decontamination, tank modifications, testing, coating and return to site.
- Provide labour for on-site flange management, and support of specialised hydrostatic testing services and prestart commissioning.
- Provide specialised administrative resources to support on site principal contract and information management.
- Provide services to construct / install well yard piping and equipment. Including connecting flowline piping.
- Apply specialised coating system, and coating integrity testing on buried flowline piping at plant, and well head connecting piping and several flow line field dig up repairs.
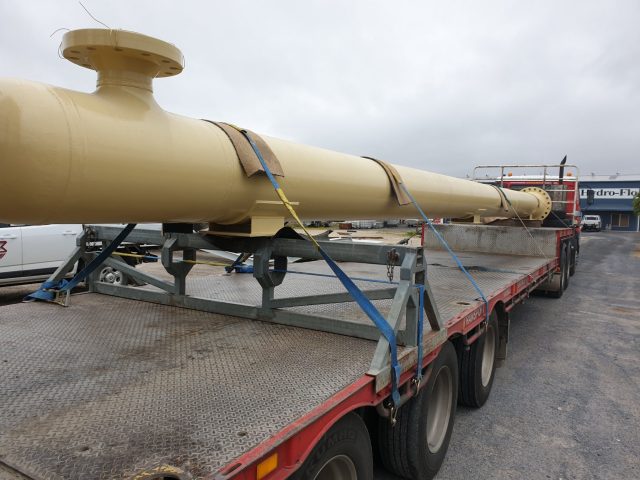
Hydrotesting of existing flowline and branches (approx. 9km)
- Strength and Leak test of flowline
- Pressure and ground temperature logged
- Hydrostatic certificates and data provided to client
Flowline cleaning and pigging
- Flushing of line with biocide dosed water
- Disposal of dosed water
- Pigging of line with a combination of brush and foam pigs
- Assessment of pipeline internal profile with gauging pig
- Intelligent pigging using 1x GPS pig and 1x radiographic pig
- Further cleaning and pigging
- Dewatering, drying and capping of line
Dig ups and coating repairs
- Excavation of coating defect areas identified during intelligent pigging
- Coating repairs using STOPAQ system
- Removal of anode beds no longer required
- Backfilling and making good of area
- Development and completion of Quality documentation
Flowline modifications (below ground)
- Dig up, removal of barred tee and capping of abandoned spur line
- Dig up, removal of barred tee and installation of risers and valves for future well extensions
- Laying of new flowline extension into new well yard
- Weld surface treatment using STOPAQ system
- Backfill and making good of surface
- Hydrotesting of modified section
- Dewatering and drying of line
Well yard install
- Installation of above ground duplex stainless well yard piping
- Installation of gas metering skid
- Installation of generator, corrosion inhibitor and other skids
- Installation and labelling of all valves and gauges
- Supply of site facilities and equipment at well yard
316 Stainless Steel Fuel Skid
Clients > Engie
Project Year > 2019 – 2020
DMK Engineering In-house Engineering, Design Fabrication of Fuel Skid.
- Fuel Oil Filtration Skid Frame
- 316 Stainless Steel Fabrication of Skid and Pipe supports
- Piping Design and fabrication to AS4041 Class 2A
- Stainless Steel Filter Vessel
- Supplied as a Turnkey Package, with completed EX rated electricals and Pressure Vessel registration
- Fire rated Valves supplied and installed
- Surface Treatment of Stainless-Steel being bead blasted for Matte Finish.
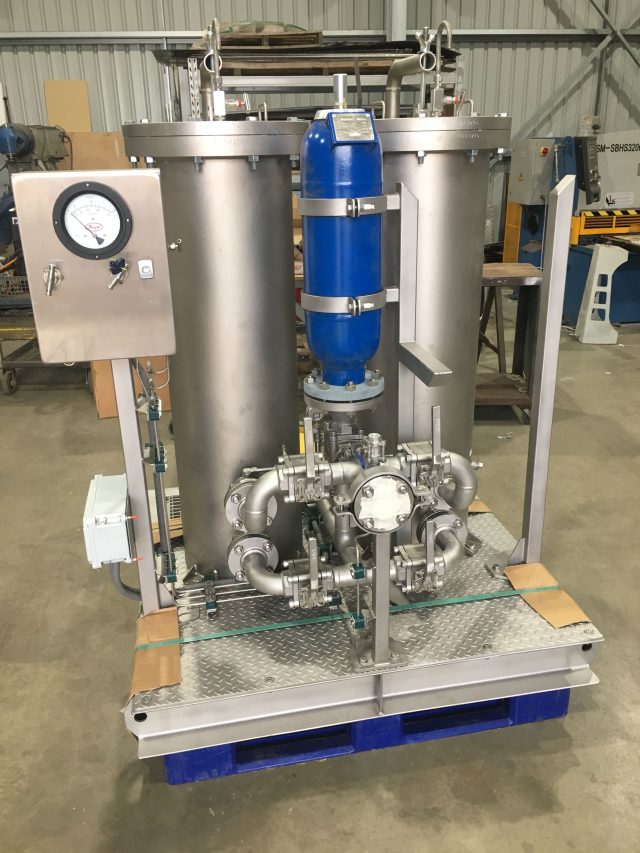
Clarke Energy – Owen Spring
Clients > Clarke Energy, Territory Generation
Project Year > 2017
DMK Engineering was Subcontracted by Clarke Energy to Manufacture, Supply and Install all power station steelwork and piping for Owen Spring Power Station expansion project in 2017. Owen Spring Power Station is approximately 20km south of Alice Springs in the Northern Territory. The project had a number of phases including manufacture and installation of the powerhouse, gas and lube oil piping, pipe supports and service air piping.
- Powerhouse Structural Steelwork
- Access Platforms
- Access Stairways
- Pipe Supports and Stands
- Cable Ladder Supports
- Lube Oil Tank Frame
- Oil Pump Skid
- Above Ground Gas and Oil Pipework
- Lube Oil Pipework
- Service Air Pipework
- Waste Coolant Pipework
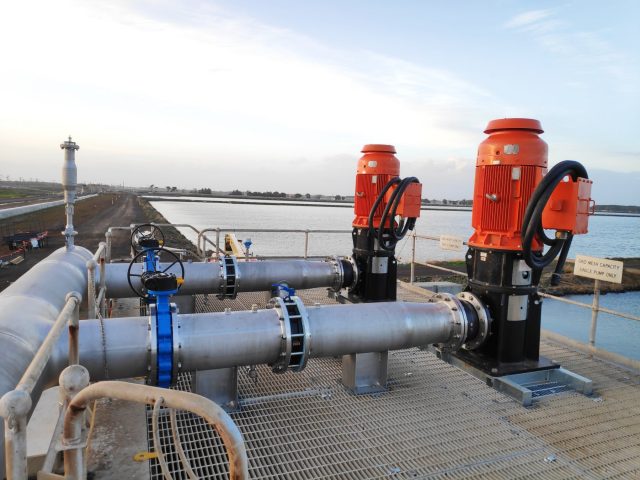
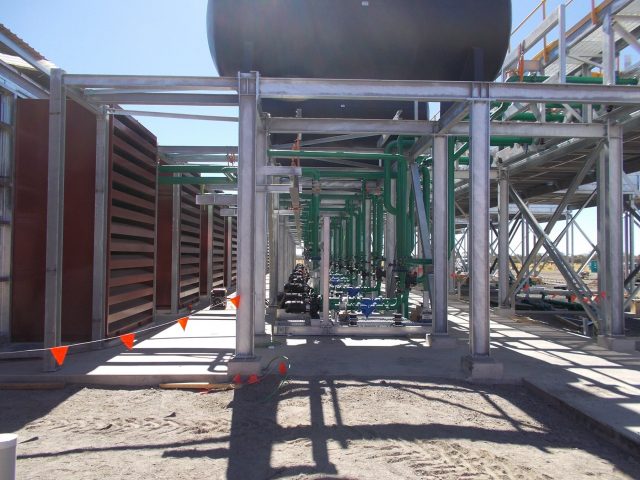